www.engenharia-brasil.com
18
'17
Written on Modified on
Abordagem prática para controlar perdas na fabricação
Os fabricantes estão sempre em busca de maneiras para maximizar a produtividade e a eficiência. Hoje em dia, esses esforços geralmente envolvem programas de alto nível que empregam palavras da moda, como computação em nuvem, fabricação orientada aos dados, sistemas físicos virtuais e Industria 4.0. Essas iniciativas avançadas são excelentes conceitos e podem produzir resultados impressionantes. No entanto, a realidade da fabricação muitas vezes interfere na implementação de tais planos ambiciosos, e uma realidade crítica é a falta de controle de resíduos no processo de fabricação. Antes de discutir digitalização e otimização, é necessário que o fabricante examine suas operações, determine onde os resíduos estão e desenvolva métodos para reduzi-lo ou eliminá-lo. O controle de resíduos é o primeiro passo na preparação de uma empresa de produção voltada à adoção de estratégias de produção inteligentes e sofisticadas. Figura 1 - imagem total de todos os elementos e como eles se relacionam e interagem em uma fábrica (PRÓXIMA ETAPA - modelo e conceito).
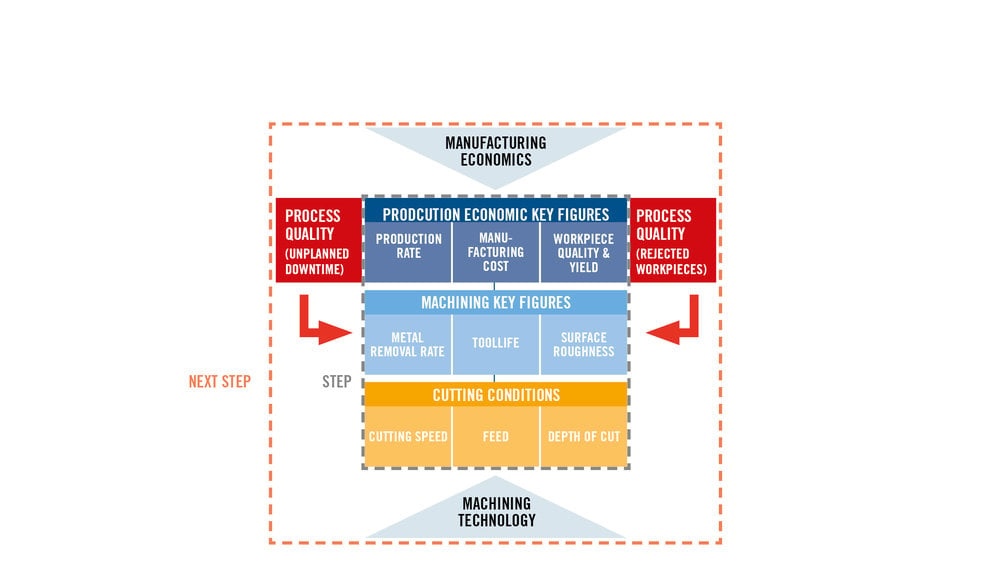
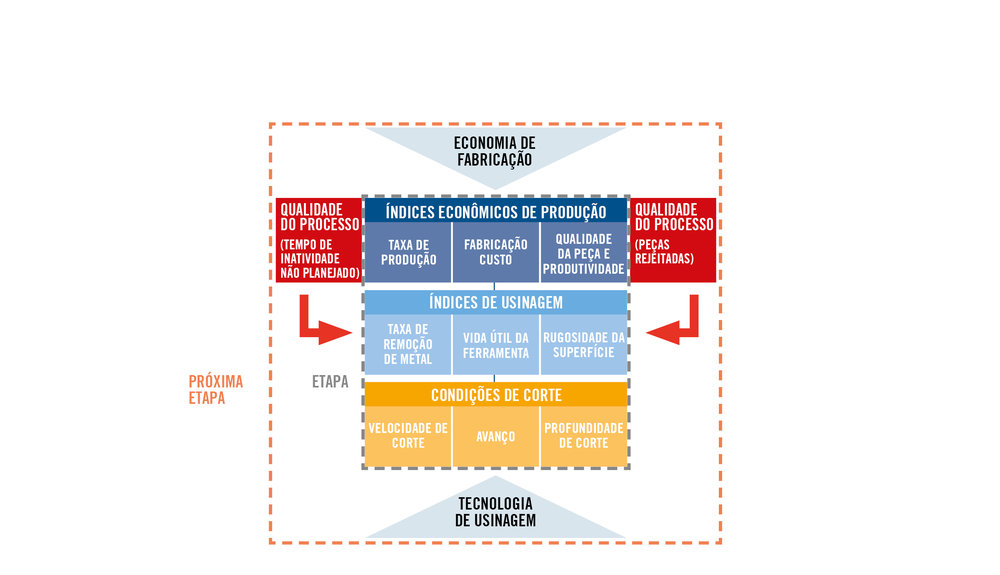
Princípios básicos de economia na produção
Fabricação consiste em uma série de processos de transformação. Uma produção transforma matéria-prima em peças acabadas ou semiacabadas através de uma série de operações de transformação individuais, como forjamento, soldagem ou usinagem. Diversos elementos compõem cada operação. Os elementos básicos de usinagem, por exemplo, incluem a ferramenta de corte, a ferramenta de usinagem, dispositivos de fixação e líquidos de refrigeração. Juntos, esses elementos formam um sistema de usinagem que tem o apoio dos equipamentos e componentes relacionados em um sistema de produção.
Funções de planejamento, programação e gestão econômica cercam o sistema de produção para formar um ambiente de produção. O elemento-chave de um ambiente de produção são as pessoas. Embora a produção hoje use amplamente computadores, robôs e outras tecnologias avançadas, as pessoas tomam as decisões que controlam o ambiente em geral.
O processo de usinagem é baseado em detalhes de aplicação técnica referentes à seleção da ferramenta, condições de corte, programação, materiais e fixação. Outros detalhes importantes incluem requisitos de volume de produção e a qualidade especificada das peças acabadas.
A associação de detalhes de aplicação técnica com preocupações econômicas é chamada de economia de produção. O objetivo da ciência da economia de produção é equilibrar todos os fatores envolvidos. Enquanto elementos técnicos produzem resultados desejados em termos de qualidade da peça, quantidade e pontualidade, as operações devem ser executadas por um custo que faça a empresa prosperar.
Encontrar um equilíbrio entre resultado e custo na usinagem é um processo de três fases. A primeira fase é estabelecer um processo de usinagem confiável. É essencial minimizar ocorrências inesperadas, tais como ferramentas quebradas, cavacos sem controle e peças que acabam destruídas. Uma produção estabelece a confiabilidade operacional, pois escolhe ferramentas com capacidade de carga que atendem ou excedem as cargas mecânicas, térmicas, químicas e tribológicas geradas no processo de usinagem.
Figura 2 - Modelo de usinabilidade total desenvolvido na ETAPA.
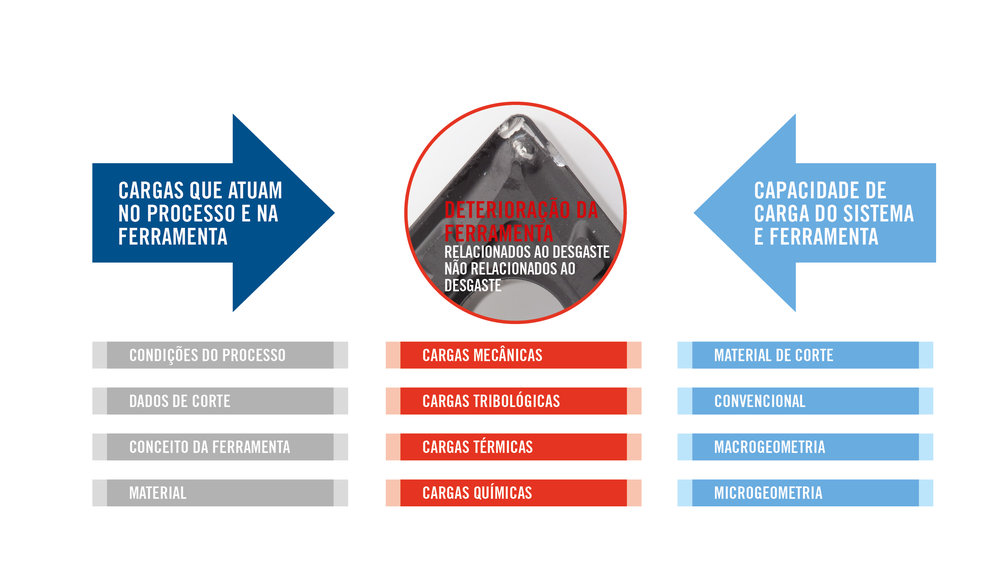
HQ_ILL_Machinability _model
A fase dois na obtenção de uma economia de produção equilibrada envolve escolher as condições de corte que refletem restrições impostas sobre o processo de usinagem por circunstâncias reais. A capacidade teórica de uma ferramenta de corte é ampla. Mas a realidade específica da produção restringe a gama de parâmetros de aplicação eficientes.
Por exemplo, os recursos e o desempenho de uma ferramenta variam de acordo com a quantidade de potência exercida pela ferramenta de usinagem que a aplica, as características de usinagem do material ou a configuração de uma peça que pode ser propensa à vibração ou distorção. Embora haja uma vasta seleção de condições de corte que funcionam na teoria, infelizmente as restrições impostas pela realidade acabam estreitando a gama de opções livres de problemas.
A Figura 3 ilustra uma grande seleção ou volume de velocidades de corte, profundidades de corte e avanços que se esculpiram em uma pequena seleção e um volume reduzido em reconhecimento de várias realidades de uma aplicação específica de corte.
Figura 3 - ilustração em 3D que mostra a coleta de todas as combinações de condições de corte que podem ser usadas dentro das limitações que vêm do ambiente de corte.
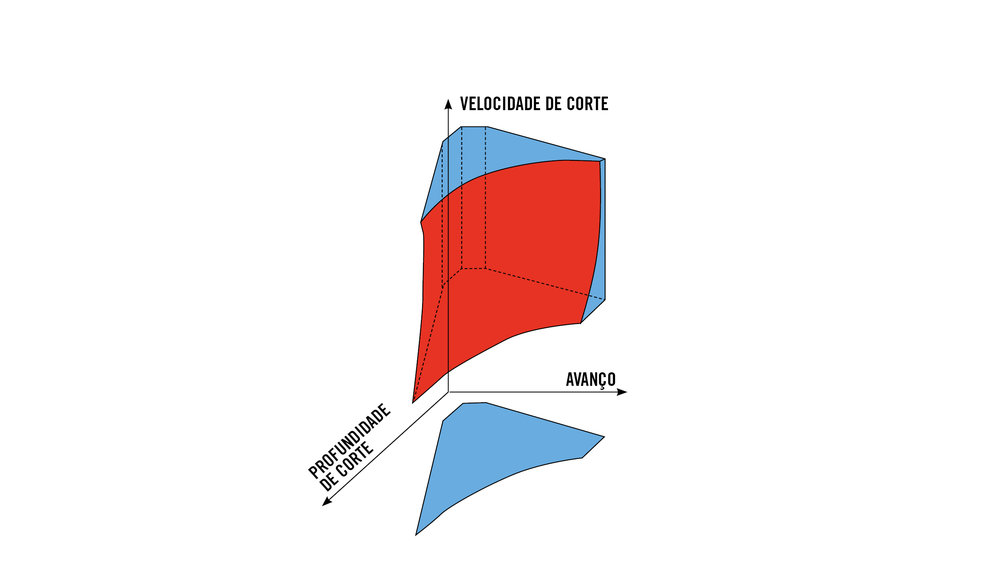
HQ_ILL_Machining_Process_cutting_conditions
Aplicar as condições de corte fora das restrições de aplicação da situação específica gera consequências econômicas negativas, incluindo custos mais altos e produtividade menor. Talvez, 90 por cento dos problemas observados durante a usinagem resultam de uma falta de respeito pelas restrições que a realidade da produção impõe sobre o processo de corte.
Quando as condições de corte não excedem as exigências impostas pela realidade da produção, a operação é segura, do ponto de vista técnico. Entretanto, nem toda combinação tecnicamente segura de condições de corte produz o mesmo resultado econômico. Alterar as condições de corte muda o custo do processo de usinagem. Passar para condições de corte mais agressivas, porém ainda tecnicamente seguras, aumenta o rendimento de peças acabadas, mas depois de certo ponto, a produtividade tende a cair, pois os parâmetros de corte mais agressivos também resultam em vida útil mais curta. O rendimento das peças ao longo do tempo também cai, pois mais tempo será necessário para a troca das ferramentas gastas.
Em algum lugar, existe uma combinação de condições de corte que resultam em um equilíbrio entre resultado produtivo e custo de fabricação. A figura 4 mostra a relação entre as condições de corte, a produtividade e os custos de ferramentas e máquinas. (O gráfico se concentra somente em elementos que variam conforme as mudanças das condições de corte - material, despesas e custos de administração e engenharia não estão incluídos.) Condições mais agressivas estão do lado direito dos eixos, e maior produtividade, na parte superior. A faixa azul-claro no meio do gráfico indica onde as condições de corte produzem uma combinação balanceada de produtividade (rendimento mais alto) e economia (custo mais baixo).
Figura 4 - relação entre as condições de corte, produtividade e custos de usinagem. Esta figura mostra um modelo simplificado, não levando em conta os fatores de resíduos.
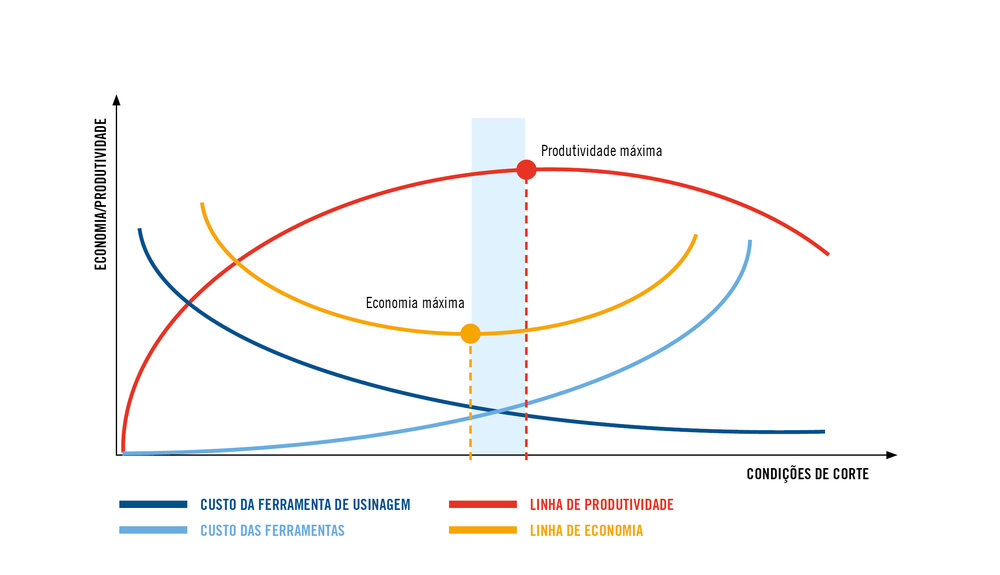
HQ_ILL_Machining_Process_relationship_cutting_conditions_productivity_machining_costs
Portanto, a terceira fase na obtenção de uma economia de produção equilibrada envolve determinar a combinação ideal de condições de corte de determinada situação. É essencial levar em conta todos os fatores nas operações de usinagem para estabelecer um domínio funcional em que os parâmetros de corte forneçam os níveis desejados de produtividade e economia.
O efeito dos resíduos sobre a economia de produção
Infelizmente, os elegantes métodos científicos de uma economia de produção equilibrada operam à mercê de resíduos no sistema de fabricação. O desperdício destrói o equilíbrio e ocorre de muitas formas. Por exemplo, é um desperdício de energia e potência quando uma ferramenta de usinagem de 60 kW é usada em uma aplicação contínua que exige apenas 15 kW. Em outra situação, quando peças acabadas não atendem aos níveis necessários de qualidade, o tempo, o dinheiro e os recursos investidos no processo são desperdiçados em busca de um resultado inaceitável. Da mesma forma, a fabricação de peças que desnecessariamente excedem níveis essenciais de qualidade é algo dispendioso, porque atingir maior qualidade faz elevar o custo.
Uma ocasião menos óbvia e menos compreendida de desperdício é a subutilização ou o mau uso de recursos intelectuais. Certas pessoas em uma empresa podem ter conhecimentos ou habilidades que ajudem a empresa a alcançar suas metas, mas, por razões que variam desde falta de comunicação até políticas intracorporativas, esses conhecimentos e habilidades não são compartilhados e, portanto, vão para o lixo.
Ferramentas de redução de desperdício
Depois que o desperdício é identificado e categorizado, a oficina deve criar um plano para reduzi-lo ou eliminá-lo. Existe uma grande variedade de ferramentas que permitem a um fabricante indicar, quantificar e minimizar práticas dispendiosas. Por exemplo, análise de uso da ferramenta, manipulação e deterioração podem apontar áreas de problemas.
Essas análises têm mostrado que, em alguns casos, de 20 a 30 por cento das ferramentas que os profissionais definiram como desgastadas, na verdade, ainda estavam viáveis - a duração restante da ferramenta era desperdiçada. Estabelecer critérios claros de desgaste da ferramenta e comunicar os padrões para o pessoal da oficina reduzem significativamente o desperdício da vida útil da ferramenta.
Da mesma forma, análises de tempo de inatividade da máquina quantificam o tempo gasto em atividades como configuração, programação e troca da ferramenta. Essas análises geralmente indicam que de 50 a 60 por cento do tempo de inatividade da máquina pode ser evitado quando se tem melhor compreensão, execução e coordenação dessas atividades necessário, porém demoradas.
O uso de entrevistas, pesquisas e programas de treinamento pode revelar muitas informações úteis ao lidar com questões de pessoal que levam ao desperdício de recursos intelectuais, bem como conhecimentos e habilidades não percebidos. Como resultado, os funcionários realizam melhor seus trabalhos e criam capabilidades que maximizam a produtividade dos funcionários.
Gerenciamento de atividades de valor agregado, valor capacitador e desnecessárias
No início do século 20, o engenheiro industrial norte-americano Fredrick Taylor estudou operações de produção e propôs que as melhorias na produtividade fossem feitas pela eliminação de todas as atividades de um processo que não agregassem valor ao produto final. As diretrizes da moderna fabricação "lean" seguem essa linha de pensamento.
Nas operações de usinagem, a única atividade real de valor agregado ocorre quando a ferramenta é de corte de metal e de produção de cavacos. Outras ações, como carregamento e fixação de peças, atividades temporárias de valor capacitador, não diretamente agregam valor para o produto fabricado, mas são necessárias para permitir que a atividade de valor agregado ocorra.
Um terceiro grupo de atividades no sistema de usinagem são as desnecessárias. Essas atividades não criam valor nem permitem sua criação, mas consomem recursos sem qualquer benefício. Elas são puramente ocasiões de desperdício. A solução de problemas é um exemplo de atividade desnecessária. Se um processo for adequadamente projetado e controlado desde o início, não haverá problemas e nenhum tempo será gasto para resolvê-los.
Figura 5 - imagem esquemática de uma produção de usinagem e todos os elementos relacionados a ela.
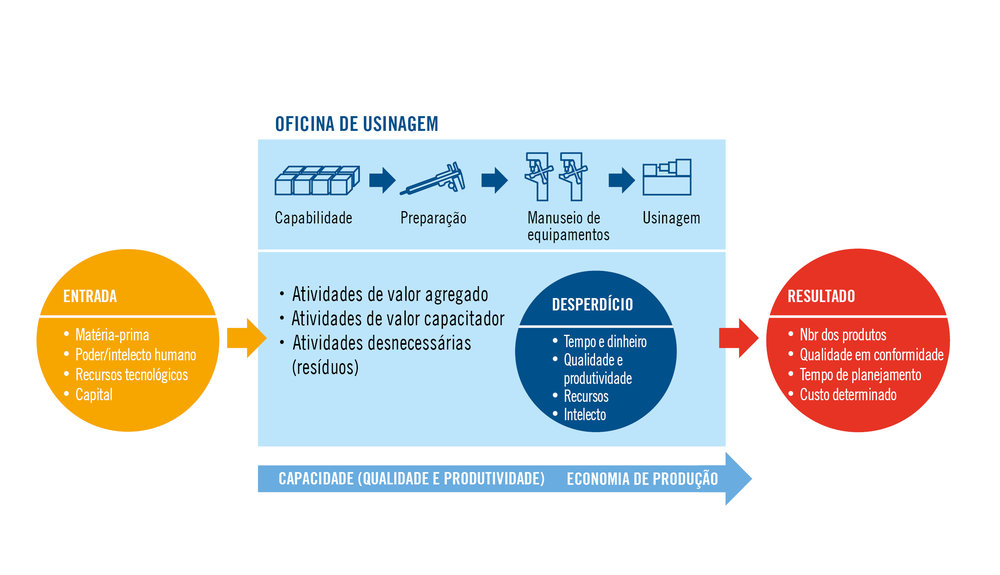
HQ_ILL_Machining_process_workshop
Conclusão
Grande parte das atividades passadas e desnecessárias foi aceita como parte do processo de fabricação e não reconhecida como grandes rompedoras da economia de produção equilibrada. Atualmente, a atenção está se voltando para a eliminação ou minimização de atividades desnecessárias. O foco da produtividade ou planejamento de capacidade recai sobre a eliminação de atividades desnecessárias, minimizar atividades de valor capacitador e otimizar as de valor agregado. (Consulte a figura 6)
Figura 6 - Visão geral de atividades de valor agregado (laranja), atividades de valor capacitador (azul) e atividades desnecessárias (vermelho). O fator humano (cinza) é o fator principal para alcançar a melhor percepção na fabricação de desempenho superior.
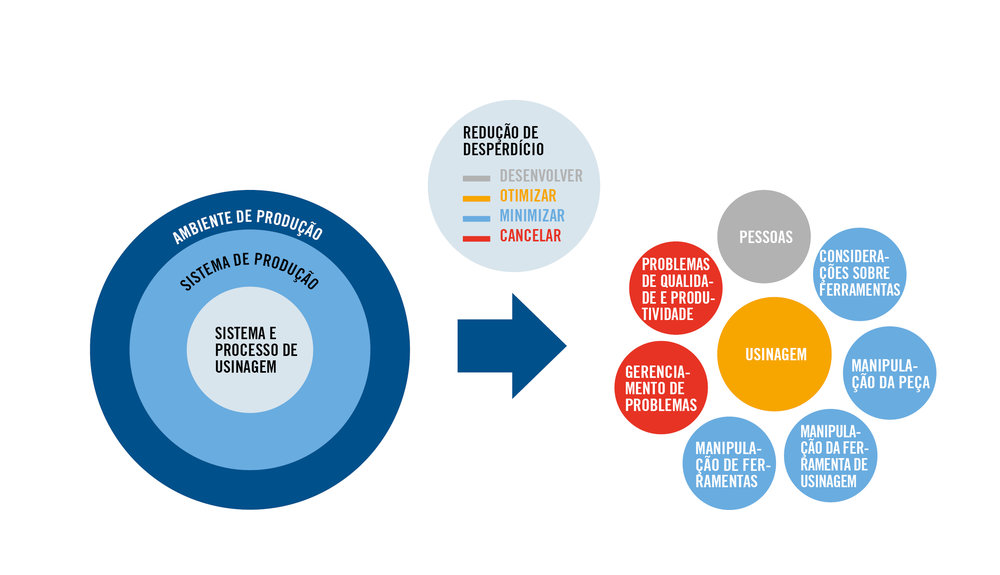
HQ_ILL_Machining_system_process
Quando o desperdício é eliminado, a economia de produção teórica se torna prática. Nesse ponto, o progresso em relação à economia de produção pode ser aplicado diretamente ao sucesso da empresa. No entanto, na tentativa de eliminar todas as ocasiões de desperdício, é necessário ter cuidado. É importante quantificar o retorno sobre o investimento das atividades de redução de desperdício. Eliminar totalmente certa incidência de desperdícios pode envolver um investimento tão grande do ponto de vista econômico que pode ser melhor aceitar o desperdício, ou parte dele, e conviver com ele. Tais decisões são tomadas depois de uma análise quantitativa apropriada, bem como dentro da empresa, sobre como elas afetarão as metas e as filosofias da empresa.
Barra lateral:
Serviços de Consultoria da Seco
Na medida em que a fabricação de produtos se torna mais sofisticada, os usuários têm mais necessidade de assistência na aplicação para obterem máximos benefícios das novas tecnologias. Na usinagem, o nível inicial de assistência é a diretriz para a seleção da ferramenta certa para determinada operação. Depois que uma ferramenta é selecionada, outras informações facilitam a escolha de condições de corte otimizadas, uso de líquido de refrigeração e outras considerações. Em seguida, se uma ferramenta não funcionar como esperado nessa operação, o fornecedor pode ajudar na solução do problema. Esses três modos de assistência compõem os serviços tradicionais da usinagem.
Quando o serviço de usinagem se expande de uma única aplicação para cobrir um processo em que uma peça está sujeita a várias operações realizadas em uma ou mais máquinas, os usuários finais precisam de orientação ao dispor a sequência de operações, manipulação de peças e outros fatores para maximizar a eficiência e a produtividade. Esse nível de assistência pode ser chamado de serviço de engenharia.
Com cada vez mais frequência os fabricantes buscam sentido para melhorar funções, resultados e controle de custos para toda uma produção ou organização. Nesses casos, algumas empresas independentes de consultoria executam o que eles descrevem como consultoria de gestão ou fabricação. No entanto, para fazer uma verdadeira avaliação de uma organização de fabricação, é essencial compreender completamente as operações centrais do negócio.
Aplicando sua longa e extensa compreensão dos processos de usinagem e conjunto de ferramentas, a Seco oferece serviços tradicionais de usinagem, serviços de engenharia e serviços de consultoria mais amplos por várias décadas. Esses serviços eram oferecidos conforme a demanda e a situação, mas, em 2016, a Seco formou seus Serviços de consultoria para oferecer aos seus clientes uma variedade mais simplificada e responsiva de serviços de fabricação.
Os serviços de consultoria da Seco incluem uma ampla gama de recursos específicos e métodos de entrega. Seleção da ferramentas e assistência na aplicação estão disponíveis on-line continuamente para poder oferecer uma resposta imediata às necessidades de produtividade do chão de fábrica.
Os serviços de engenharia podem começar com a comunicação eletrônica e estender-se até visitas ao local, se necessário. Os Serviços de consultoria da Seco também incluem análise abrangente e orientação envolvendo a operação de todas as funções em uma produção. Esses serviços podem incluir consulta de manutenção da ferramenta de usinagem, layout da produção, logística e funções organizacionais. Conselhos sobre questões de habilidades e conhecimentos das pessoas e a relação entre as técnicas de fabricação empregadas com as estratégias de produção da organização e considerações de custos podem também ser incluídos.
Cada relacionamento de Consultoria da Seco se baseia no conceito NEXT STEP, mas também é personalizado conforme as necessidades específicas da organização participante, além de existir um diálogo entre a Seco e o cliente com o foco em um objetivo comum.