www.engenharia-brasil.com
21
'10
Written on Modified on
A Genzyme monitoriza 50 000 pontos SCADA com o sistema Anybus Communicator
A empresa, líder mundial em biotecnologia, encontra-se a criar um novo local de produção de anticorpos policlonais. Esta é uma unidade de produção inovadora: o processo foi automatizado tanto quanto possível, de modo a reduzir a possibilidade de erro humano nas diversas fases do processo (separação, purificação, ultrafiltração, hemadsorção etc.). Isto requer a capacidade de funcionar como interface com um conjunto de equipamento laboratorial muito diverso que não foi concebido inicialmente para comunicar com buses de campo. A Genzyme utilizou cerca de trinta gateways HMS Anybus Communicator de forma a possibilitar uma gestão SCADA consistente em todos os dispositivos em utilização. Isto traz benefícios tanto em termos de qualidade como de custos de produção.
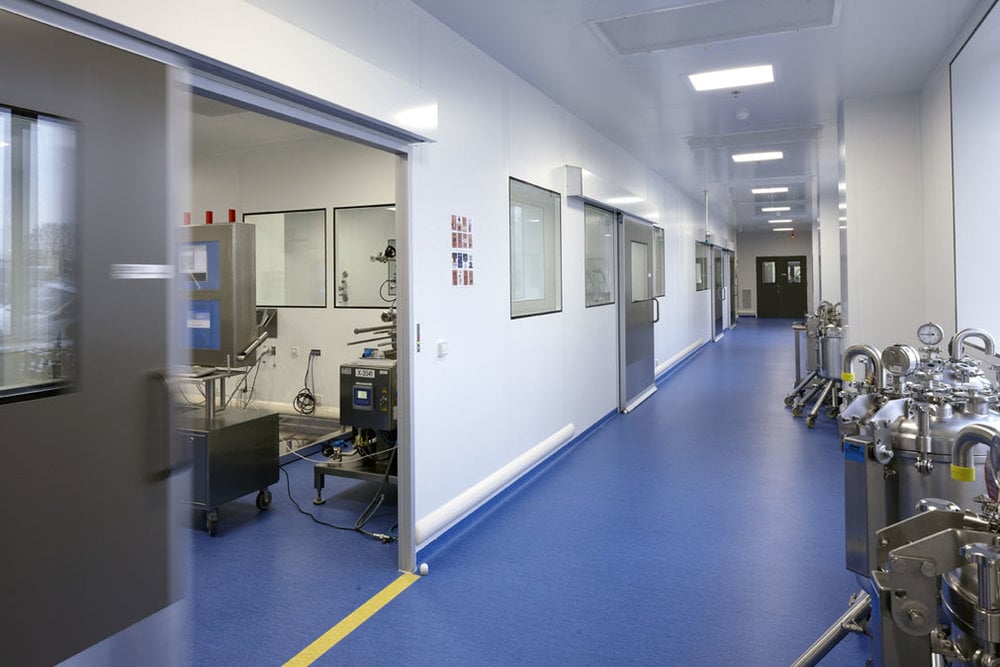
A unidade de bioprodução de Lyon estende-se por uma área de 22 000 m², produzindo um imunossupressor selectivo utilizado para evitar e tratar a rejeição de órgãos durante os transplantes (Timoglobulina®).Este fármaco também é utilizado em hematologia, nos casos onde as células transplantadas reagem contra o doente transplantado em situação de transplante de medula óssea. Os agentes activos deste fármaco são as imunoglobulinas timocitárias anti-humanas, obtidas a partir da purificação de um soro, que é utilizado como matéria-prima. A base imunogénica é composta por timócitos (células do timo), uma fonte natural de células T. O desenvolvimento desta unidade compreendeu um investimento avaliado em 115 milhões de euros. «A Genzyme encontra-se actualmente a utilizar métodos de produção que requerem mão-de-obra intensiva na Sanofi Pasteur, em Marcy. Com a nova unidade, esperamos optimizar o processo de modo a reduzir ao máximo a possibilidade de erro humano. Este processo por lotes altamente sequencial engloba mais de 780 etapas de produção. Há muitas fontes de erro. A automatização de um processo deste género requereu bastante trabalho em proximidade com o equipamento envolvido aquando da decisão acerca do comportamento do sistema. Isto fez com que se evitasse repensar toda a ergonomia do edifício e do equipamento de produção, ao mesmo tempo que ainda se criava uma verdadeira revolução no funcionamento do processo de produção. De modo a atingir este objectivo, especificámos mais de 4 000 parâmetros e 13 000 alarmes, fazendo com que conseguíssemos dominar todas as etapas de produção,» explica Alexis Ducancel, responsável na Genzyme pelos Sistemas Automatizados.
Bioprodução: uma série de processos complexos
Ao contrário da química tradicional, a produção baseada em células vivas implica muitas etapas complexas e dispendiosas diferentes. O ciclo de produção de uma proteína recombinante requer uma infraestrutura industrial com capacidade para uma produção em grande escala, envolvendo diversas etapas escalonadas por diversos meses. Cada etapa está sujeita a numerosos controlos de qualidade. Realiza-se análises durante o ciclo de produção para assegurar a ausência de vírus e de contaminantes. No final, também se verifica a pureza e a acção da proteína. A produção deste fármaco implica muitas etapas de produção complexas, marcadas por uma sucessão de testes técnicos e de garantia de qualidade. O processo de produção pode ser dividido em quatro etapas principais:
-A colheita de imunoglobulinas, realizada injectando tecido humano em coelhos.
-A purificação das imunoglobulinas para retirar proteínas indesejadas (em particular, anticorpos anti-eritrocitários), por hemadsorção.
-A etapa de cromatografia consiste numa troca de aniões através da utilização de uma resina de troca de iões. As impurezas são capturadas pela resina, ao passo que as imunoglobulinas, não possuindo uma carga negativa, são eluídas. Esta etapa é verificada através de espectrofotometria e electroforese.
-A etapa de precipitação destina-se a eliminar as últimas impurezas que ainda restem. As imunoglobulinas purificadas são pasteurizadas (60°C durante 10 horas). Esta solução é liofilizada antes de ser fechada em frascos. «Neste processo, podemos, por exemplo, configurar as centrifugadoras (velocidade, temperatura, tempo de funcionamento, etc.). Estes valores podem ser alterados no SCADA de modo a tomar em consideração requisitos específicos do lote de produção actual. Fazem-se leituras em todas as etapas, sendo depois reenviadas para o SCADA. Isto dá-nos a possibilidade de implementar um processo de rastreabilidade muito preciso. Em particular, isto significa uma redução significativa da carga de trabalho entregue às equipas de garantia de qualidade, o que representa uma vantagem em termos de custos,» refere Alexis Ducancel. A unidade de Lyon, tal como a de Marcy, irá receber a aprovação da FDA e da AFFAPS. «Naturalmente, escolhemos a HMS porque sentimos que nenhuma outra empresa disponibilizava soluções padrão para o reenvio de dados a partir de um conjunto de equipamento muito heterogéneo que não tenha sido necessariamente concebido para a ligação a buses de campo. Temos 28 centrifugadoras, medidores de pH e balanças, entre outros equipamentos. Os protocolos de interface variam: de série ou ASCII, por exemplo. Os 30 Anybus Communicators no local reenviam os dados por Ethernet ou Profibus para o SCADA central.»
Anybus Communicator: a solução para integrar equipamento de série na rede de comunicação industrial
A gama de gateways Anybus Communicator de ligação a Ethernet/Bus de Campo industrial possibilita a ligação à rede de dispositivos que foram desenvolvidos para a utilização numa rede de série. O Anybus Communicator tem a capacidade de ligar a maioria dos produtos com interface de série RS-232/422/485 a uma Ethernet ou bus de campo industrial. Realiza uma conversão inteligente entre o protocolo de série e a rede de destino. A configuração desta conversão é efectuada mediante o uso do software »ABC Config Tool». A configuração da rede, depois de completa, pode ser reutilizada em todas as redes suportadas pelo Communicator. «Não mencionando novamente a elevada qualidade do produto, é certo que o apoio técnico estava presente sempre que precisávamos,» conclui Alexis Ducancel. Já foram colocados cerca de cinquenta colaboradores no local de produção da Genzyme, onde os lotes de produção iniciais estão a decorrer para que se valide o processo de produção. A plena produção deverá começar nos finais de 2011, depois de se ter obtido as certificações da AFSSAPS. O número total de colaboradores deverá, então, ascender aos 270.
Bioprodução: uma série de processos complexos
Ao contrário da química tradicional, a produção baseada em células vivas implica muitas etapas complexas e dispendiosas diferentes. O ciclo de produção de uma proteína recombinante requer uma infraestrutura industrial com capacidade para uma produção em grande escala, envolvendo diversas etapas escalonadas por diversos meses. Cada etapa está sujeita a numerosos controlos de qualidade. Realiza-se análises durante o ciclo de produção para assegurar a ausência de vírus e de contaminantes. No final, também se verifica a pureza e a acção da proteína. A produção deste fármaco implica muitas etapas de produção complexas, marcadas por uma sucessão de testes técnicos e de garantia de qualidade. O processo de produção pode ser dividido em quatro etapas principais:
-A colheita de imunoglobulinas, realizada injectando tecido humano em coelhos.
-A purificação das imunoglobulinas para retirar proteínas indesejadas (em particular, anticorpos anti-eritrocitários), por hemadsorção.
-A etapa de cromatografia consiste numa troca de aniões através da utilização de uma resina de troca de iões. As impurezas são capturadas pela resina, ao passo que as imunoglobulinas, não possuindo uma carga negativa, são eluídas. Esta etapa é verificada através de espectrofotometria e electroforese.
-A etapa de precipitação destina-se a eliminar as últimas impurezas que ainda restem. As imunoglobulinas purificadas são pasteurizadas (60°C durante 10 horas). Esta solução é liofilizada antes de ser fechada em frascos. «Neste processo, podemos, por exemplo, configurar as centrifugadoras (velocidade, temperatura, tempo de funcionamento, etc.). Estes valores podem ser alterados no SCADA de modo a tomar em consideração requisitos específicos do lote de produção actual. Fazem-se leituras em todas as etapas, sendo depois reenviadas para o SCADA. Isto dá-nos a possibilidade de implementar um processo de rastreabilidade muito preciso. Em particular, isto significa uma redução significativa da carga de trabalho entregue às equipas de garantia de qualidade, o que representa uma vantagem em termos de custos,» refere Alexis Ducancel. A unidade de Lyon, tal como a de Marcy, irá receber a aprovação da FDA e da AFFAPS. «Naturalmente, escolhemos a HMS porque sentimos que nenhuma outra empresa disponibilizava soluções padrão para o reenvio de dados a partir de um conjunto de equipamento muito heterogéneo que não tenha sido necessariamente concebido para a ligação a buses de campo. Temos 28 centrifugadoras, medidores de pH e balanças, entre outros equipamentos. Os protocolos de interface variam: de série ou ASCII, por exemplo. Os 30 Anybus Communicators no local reenviam os dados por Ethernet ou Profibus para o SCADA central.»
Anybus Communicator: a solução para integrar equipamento de série na rede de comunicação industrial
A gama de gateways Anybus Communicator de ligação a Ethernet/Bus de Campo industrial possibilita a ligação à rede de dispositivos que foram desenvolvidos para a utilização numa rede de série. O Anybus Communicator tem a capacidade de ligar a maioria dos produtos com interface de série RS-232/422/485 a uma Ethernet ou bus de campo industrial. Realiza uma conversão inteligente entre o protocolo de série e a rede de destino. A configuração desta conversão é efectuada mediante o uso do software »ABC Config Tool». A configuração da rede, depois de completa, pode ser reutilizada em todas as redes suportadas pelo Communicator. «Não mencionando novamente a elevada qualidade do produto, é certo que o apoio técnico estava presente sempre que precisávamos,» conclui Alexis Ducancel. Já foram colocados cerca de cinquenta colaboradores no local de produção da Genzyme, onde os lotes de produção iniciais estão a decorrer para que se valide o processo de produção. A plena produção deverá começar nos finais de 2011, depois de se ter obtido as certificações da AFSSAPS. O número total de colaboradores deverá, então, ascender aos 270.
Figura 1:
A nova unidade da Genzyme para a produção de anticorpos policlonais para transplantes e hematologia ocupa 22 000 m². Representou um investimento avaliado em 115 milhões de euros.
Figura 2:
A gama Anybus Communicator possibilita o reenvio de dados de série para o sistema de controlo central.