www.engenharia-brasil.com
29
'22
Written on Modified on
O MAIOR DESAFIO PARA A INDÚSTRIA AUTOMOBILÍSTICA É ACOMPANHAR A EVOLUÇÃO DA TECNOLOGIA
Os nove pilares da Indústria 4.0 permitem criar conexões entre equipamentos, mas o rápido desenvolvimento tecnológico pode ser um entrave para quem ainda não se adaptou.
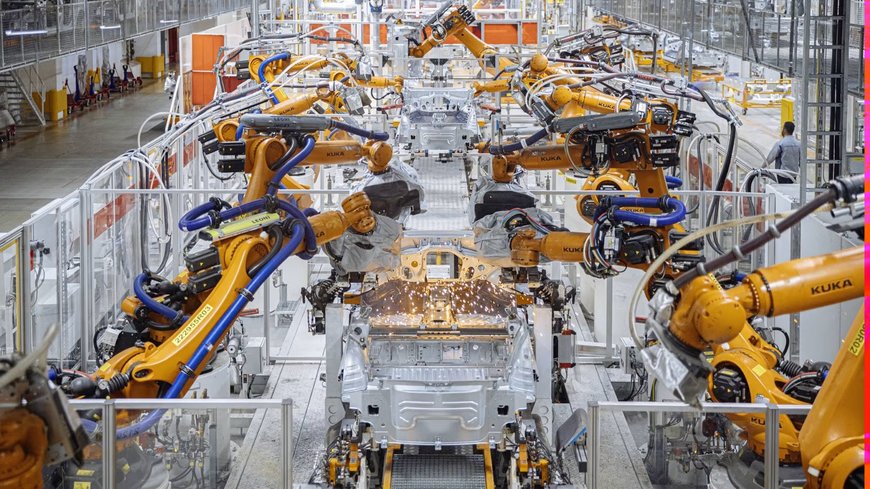
Nos últimos anos, a Industria 4.0 tem evoluído muito rápido no Brasil, especialmente no setor Automotivo, que, com altos investimentos em seus processos vem buscando maior produtividade, com mais automação e eficiência.
Porém, para Gerente Executivo do Planejamento de Manufatura da Região SAM da Volkswagen do Brasil, Fabricio Valerio, determinar o estágio em que o Brasil se encontra na quarta revolução requer um trabalho de análise mais minucioso de cada nicho.
Contudo, o executivo ressalta que, mais importante do que escalar o nível da Indústria 4.0 no País, é estar focado nos principais elementos que tornam este conceito possível.
“Na Volkswagen buscamos avançar em cada novo projeto, sempre com foco nos nove pilares da Indústria 4.0: Segurança da Informação, Realidade Aumentada, Big Data, Robôs Autônomos, Simulações, Manufatura Aditiva, Sistemas Integrados, Computação em Nuvem e Internet das Coisas. Podemos dizer que no Brasil, a VW já tem conhecimento e mão de obra especializada em todos eles, alguns em maior grau de maturidade do que outros, e entendemos estar no estágio em que não adotamos mais a tecnologia de forma isolada, mas que desenvolvemos ainda mais conectividade de uma para a outra, permitindo que as tecnologias interajam entre si e que os dados estejam conectados entre os processos”, afirma Fabricio.
Valerio ressalta que este processo permite tomadas de decisões mais assertivas. “As novas gerações de robôs já têm dados disponíveis para subir para um datalake (repositório para armazenamento de dados estruturados e não estruturados) e serem analisados com algoritmos de predição, que nos avisam sobre possíveis falhas ou tendências de qualidade no processo. Com isso, caminharemos para um estágio em que poderemos ter 100% dos nossos processos de desenvolvimento, planejamento e produção conectados para, assim, termos uma grande nuvem de dados que nos auxiliarão nas resoluções”.
Mas, assim como sua importância, inserir a Indústria 4.0 nas empresas traz grandes desafios, especialmente quando falamos do fator tecnológico.
“O maior desafio para a indústria é acompanhar a evolução do mercado, pois cada vez mais as tecnologias têm se desenvolvido de forma mais rápida. Engana-se estar à frente quem começou lá atrás implementando as tecnologias. Tudo depende do grau de comprometimento e da mudança de mindset de toda a empresa, pois é necessário se adequar à nova cultura, mais digitalizada e menos centralizada no homem. Para isso, a melhor alternativa é sempre começar por tecnologias que já alcançaram um grau de maturidade no mercado, que já passaram pelo pico das expectativas infladas. Ou seja, investir em uma tecnologia já implementada por muitas empresas, além de oferecer dados de resultados, diminui os desafios de desenvolvimento e implementação. Além disso, os cenários econômicos mundiais são complexos e exigem, por vezes, segurar investimentos. Neste caso, o que pode ser feito é buscar alternativas para tratar dados e automatizar processos nos campos que mais dominamos. É assim que fazemos aqui na VW”, orienta o Fabricio.
Impactos positivos da Indústria 4.0
Há mais de 15 anos, a Volkswagen vem utilizando as ferramentas tecnológicas da Industria 3.0 e 4.0, iniciando com Automação Industrial, com simulações virtuais e alguns sistemas integrados de produção.
Nos dias atuais, o foco da empresa tem sido na implementação de outras tecnologias, como IoT (Internet das Coisas) e Computação em Nuvem.
“Existe uma grande ação do grupo Volkswagen em criar uma Nuvem Volkswagen, conhecida internamente como DPP (Digital Production Platform), que permite a conexão dos processos nas áreas produtivas, que permitirá avanços com Big Data, IoT e robôs autônomos. Por outro lado, utilizamos bastante as simulações em processos de layout, de comissionamento e de montagem; no fluxo logístico; tempos-ciclo; e, também, de ergonomia. Atualmente, temos trabalhado em um posto de sequenciamento de peças para implementar o uso da realidade aumentada em escala. Nossa equipe de manutenção já tem na palma da mão um smartphone para consultar ordens de serviço do SAP, dados de equipamentos e outras informações. A Cyber-segurança é um outro tema em avanço rápido. Além de demandas de novas legislações, como a UNECE 155, internamente temos nosso IT-Shopflor em constante monitoramento, afinal, estando conectados, riscos de ataques hackers são reais”, revela Valerio.
‘A KUKA vem trabalhando em conjunto com diversas plantas do Grupo Volkswagen no mundo, na implementação de soluções via sistema DPP para os seus robôs industriais, com o KDC (KUKA.DeviceConnector) que é uma tecnologia que possibilita o acesso de informações do sistema do robô KUKA através dos protocolos OPCUA e MQTT; além das informações definidas na especificação VDMA40010, é possível ter acesso a diversas outras informações como sinais de comunicação, transferências de arquivos, mensagens, condições de monitoramento e segurança além do gerenciamento dos equipamentos instalados nas plantas de produção”, informa Vagner Valentim, responsável da KUKA para o Grupo VW na América do Sul.
“Sem dúvida, o principal resultado que a Indústria 4.0 pode trazer para a empresa é manter a competividade com seus concorrentes e garantir produtos e processos inovadores para os clientes. Ter começado lá atrás, quando ainda pouco se falava de Indústria 4.0, nos permitiu ter uma ampla vantagem para poder, realmente, entender que não só as tecnologias precisam ser conhecidas como, também, difundidas. Processos de realidade aumentada, ou de manufatura aditiva, são conhecidos por engenheiros, planejadores, bem como por nossos operadores do chão de fábrica e de todos os níveis. A tecnologia já está “democratizada” e enraizada em nossa cultura e processos e, mostrando o potencial e os benefícios da implementação dessas tecnologias a curto, médio e longo prazo, superamos o nosso maior desafio de quebrar a barreira do convencimento e da aceitação das novas tecnologias por parte dos nossos funcionários”, relata Fabricio.
Na VW, a capacitação dos colaboradores começa pelo ganho de confiança, mostrando que a tecnologia não substituíra a mão de obra, mas que trará benefícios para as atividades desenvolvidas.
“Em muitos casos, ressaltamos que as tecnologias permitirão dedicação para outras atribuições e não somente em processos manuais. Uma vez mostrado que a tomada de decisão vem do nosso conhecimento e que a máquina, a tecnologia ou o processo digitalizado, não serão substitutos, e que a experiência do colaborador é essencial, eu consigo ganhar a confiança dele para permitir que essa tecnologia seja inserida em seu contexto de trabalho”, reitera o Valerio.
Em um mercado tão globalizado como a Indústria Automobilística investir em tecnologia e melhorias de processos é fundamental para manter a competitividade. “Nos últimos 15 anos, já investimos milhões de euros em automação e digitalização dos nossos processos, para termos ambientes virtuais que nos permitam tomar decisões em todas as plantas do Brasil, sem a necessidade de estudos e testes in loco, simplesmente simulando processos novos, sem impactos na produção”, exemplifica o executivo da VW.
E neste caminho, a montadora segue rumo a Indústria 5.0, com a implementação inicial de pequenas ações que, futuramente, farão a diferença. “Ainda temos alguns desafios pela frente, mas estamos mudando nossos processos internos e cultura para adequarmos cada vez mais a integração de espaços multidisciplinares, ambientes coworking, além de entender que em um futuro não tão distante, estaremos trabalhando com humanos e inteligência artificial de forma natural e dentro do nosso fluxo diário”, revela.
A importância da robótica
“A robótica está presente em praticamente todos os processos de manufatura dentro da VW do Brasil, desde a Estamparia até a Montagem Final, passando pelas operações colaborativas. Temos trabalhado em estudos para automação da logística, incluindo operações robotizadas, como gerenciamento dos supermercados internos (sequenciamento de peças para a linha de montagem). Ainda, a robótica se integra completamente às ferramentas de simulação e comissionamento”.
Muitos não sabem, mas a parceria entre o Grupo Volkswagen e a KUKA é histórica e inicia-se no ano de 1956 com a instalação da primeira linha de soldagem a ponto na Alemanha, comenta Vagner.
Na América do Sul a parceria toma força a partir do início dos anos 90, tendo como ápice nesta década a instalação da fábrica da Volkswagen do Brasil em São José dos Pinhais no estado do Paraná onde a KUKA forneceu os robôs industriais. De lá até os dias atuais a KUKA se fez presente em praticamente todos os projetos em várias plantas; seja através do fornecimento de robôs, serviços de pós-vendas como peças e treinamentos ou mesmo através do projeto e instalação de linhas completas de produção para o Planejamento de Manufatura da Volkswagen para a região América do Sul, finaliza Fabricio Valerio.
www.kuka.com