www.engenharia-brasil.com
08
'19
Written on Modified on
Imprimindo em 3D o futuro das ferramentas para mobilidade elétrica
Kennametal desenvolve ferramenta leve para furo de estator impresso em 3D que atende aos requisitos de exatidão, redondeza e acabamento de superfície.
A Kennametal desenvolveu uma ferramenta para furo de estator impresso em 3D especificamente projetada para atender às exigências cada vez maiores dos clientes em termos de soluções de ferramentas mais leves para usinagem de componentes para veículos híbridos e elétricos.
Os componentes para mobilidade elétrica são normalmente usinados em centros de usinagem CNC com pouca potência que requerem soluções de ferramentas mais leves. A ferramenta para furo de estator impresso em 3D da Kennametal pesa metade da versão de fabricação convencional mas também atende aos requisitos de precisão, circularidade e acabamento de superfície para furação de carcaças de motores de alumínio.
"O furo principal, que aloja o estator de um motor elétrico, tem aproximadamente 250 mm de diâmetro (9,84") e 400 mm (15,74") de comprimento e possui um furo de rolamento menor na parte inferior", disse Harald Bruetting, diretor de Engenharia de Programação. "Se fabricado com recurso a técnicas convencionais, um alargador para esse tipo de aplicação pesaria mais de 25 quilogramas (55 lb.), um peso excessivo para as máquinas-ferramenta existentes ou para os operadores que trabalhariam com a ferramenta."
Bruetting e o Solution Engineering Group da Kennametal contaram com a capacidade de fabricação interna de aditivo da empresa para imprimir em 3D uma ferramenta indexável resistente mas leve, equipada com tecnologias Kennametal comprovadas, incluindo insertos para alargamento RIQ finos ajustáveis para acabamentos de alta precisão e um adaptador KM4X para o máximo de rigidez. A ferramenta também apresenta canais de refrigeração internos impressos em 3D que ajudam a maximizar a produtividade e a vida útil.
"Usando impressão 3D em cama de pó de metal em conjunto com software de análise de elementos finitos, conseguimos projetar e construir uma ferramenta que aproximou muitíssimo o momento de inércia da face do fuso, aumentado sua rigidez e respeitando simultaneamente as restrições de peso dos clientes", disse Werner Penkert, gestor de Soluções para o Futuro. "Trata-se de um excelente exemplo de como a Kennametal está usando tecnologia de fabricação avançada para ajudar a superar os desafios únicos dos nossos clientes."
Foram criadas duas versões da ferramenta - uma com um tubo de fibra de carbono e outra com um tubo de metal impresso em 3D. Os resultados foram impressionantes. A ferramenta com o tubo impresso em 3D apresentou um peso de 10,7 kg (23,6 lb.) e a versão de fibra de carbono 9,5 kg (20,9 lb.) - menos de metade do peso dos respectivos equivalentes convencionais.
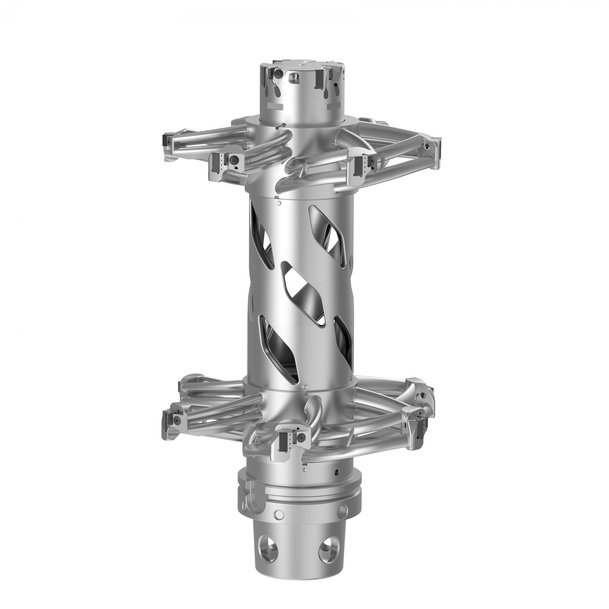
Tirando partido das tecnologias comprovadas da Kennametal. Insertos para alargamento RIQ de alta precisão e adaptador KM4X para o máximo de rigidez possível.
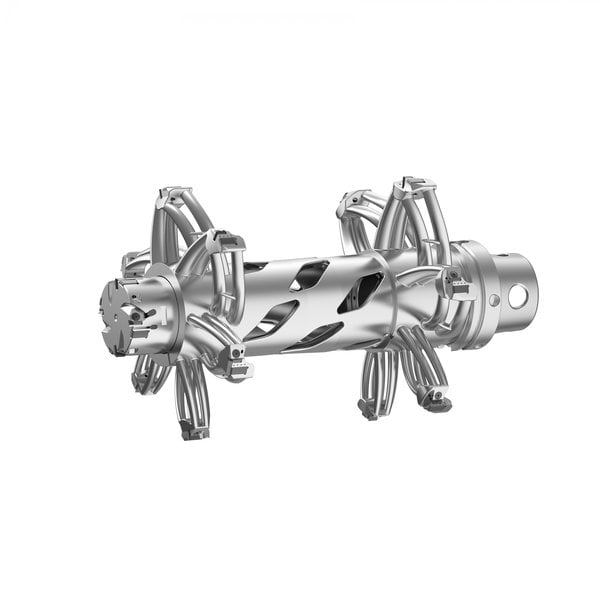
Redução de peso graças à fabricação de camada de aditivo. Impresso em 3D, peso total de 10,7 kg. Metade do peso, satisfação dos requisitos de qualidade, redondeza e precisão das superfícies dos furos para estatores.
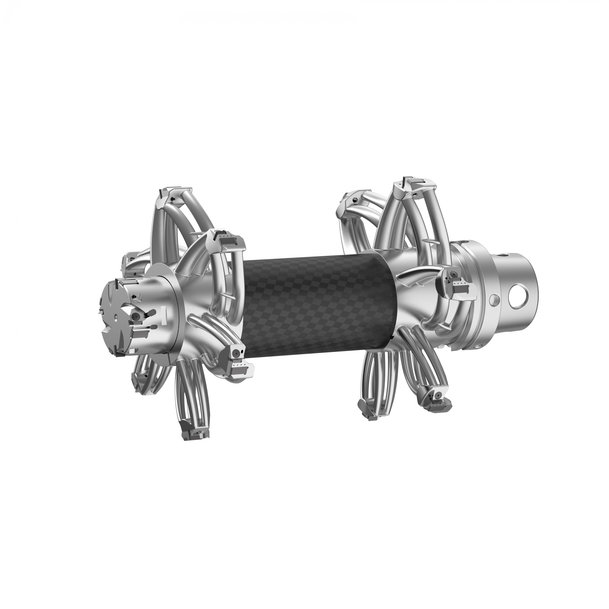
A mesma ferramenta ainda mais leve. Ao invés de com um tubo metal impresso em 3D, foi usada uma versão da ferramenta com um tubo de fibra de carbono. Redução de peso ainda maior, até 9,5 kg.